Spetec Gesellschaft für Labor- und Reinraumtechnik mbH
Address
Spetec Gesellschaft für Labor- und Reinraumtechnik mbH
Am Kletthamer Feld 15
85435 Erding
Germany
Telephone+49 8122 959090
Fax+49 8122 9590955
Discover more from us
About us
Spetec GmbH, located in Erding near Munich/Germany, is a manufacturer of cleanroom technology, laser safety and a leading supplier of peristaltic pumps.
The requirements in respect of the cleanliness of environments have increased dramatically, particularly in the areas of industrial production, photonics, biotechnology, medicine, packaging and in laboratories and research. A particulate-free, sterile environment is often crucial in such fields. And Spetec GmbH has developed a broad range of clean room solutions. Spetec GmbH supplies custom solutions for these demands, from mobile laminar flow boxes to complex turnkey clean room systems. Spetec GmbH also offers maintenance and certification of clean room systems in accordance with DIN ISO.
Based on many years of experience in clean room technology, the area of laser safety business has emerged. Individual laser safety systems are offered according to customer requirements. Innovative, application-oriented products are created through the combination of in-house development, design and fabrication combined from one single address.
In the field of laboratory technology, Spetec manufactures custom OEM pumps and standalone peristaltic pumps. A wide range of different types of tubing is also available for sale. A wide selection of single-element and multi-element standards is also available. Thanks to the highest quality and precision, Spetec became the leading supplier of peristaltic pumps.
Spetec provides customized products that can be tailored to your needs and specifications.
Keywords
- Reinraum
- Reinraumtechnik
- cleanroom
- Reinraumplanung
- Laminar Flow
Our Products
SPETEC® cleanroom cell
Cleanroom technology can be used in the manufacture, storage of dust-sensitive mechanical and electronic components, packaging and wherever a particle-free environment is needed.
Spetec has extended its cleanroom offering to encompass three different cleanroom concepts. It is possible to implement solutions for the whole range of requirements, from inexpensive installations right up to top-class cleanrooms compliant with the GMP guidelines for the pharmaceuticals industry.
The cell itself is enclosed by an odorless plastic strip curtain or side panels made from acrylic or laminated glass or aluminum sandwich panels, resulting in a self-contained unit. Other optional features are also available, such as electric sliding doors or airlocks for material or personnel, which can be fitted with a mutual locking system if required.
The effective cleanroom area anywhere between 3 m² and around 350 m² can be varied by combining individual laminar flow modules of different sizes. It is even possible to integrate assembly lines or conveyors in the cleanroom cell.
The SPETEC® cleanroom cell uses H14 filters. These have a filtration efficiency of 99.995 %. The filter captures at least 99.995 % of all particles of a size of 0.12 μm (as per MPPS). The filtration efficiency is approx. 99.9995 % for particles with a size of 0.3 μm. This laminar airflow below the flow modules means that there is no crossover with dirty air from the outside.
Using a SPETEC® cleanroom cell can, for example, reduce the particle concentration from approx. 15 million/m3 (at a size of 0.12 μm, MPPS) to approx. 1,500 particles within the unit. This corresponds to the cleanroom class 5 as per DIN ISO 5 or class 100 as per US Federal Standard 209E.
It is also possible to meet the requirements of ISO classes 5 through 9 (DIN ISO 14644-1) and classes A through D of the GMP standard. Depending on the precise requirements, SPETEC® cleanroom cells can be adapted to meet the customers’ needs.
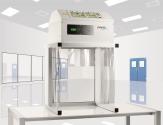
CleanBoy® - Cleanest air in the smallest space
A clean environment - i.e. free of particles and germs - plays an increasingly important role in various branches of industry.
Particularly in working areas where airborne dust particles can lead to manufacturing defects or poor quality and thus to financial losses, it consequently seems necessary to set up clean rooms whose purchase and maintenance are often associated with high costs.
However, it is not necessarily a must to build such costly and technically complex rooms - it is often just sufficient to create clean room conditions for a restricted sub-area.
Spetec's cleanroom technology aims to remove particles with a diameter of 0.12 µm and larger in the narrowest of spaces, where the highest cleanliness standards must ensure a reliable process flow. Spetec's mobile, ready-to-use cleanroom devices can be used for the assembly or storage of dust-sensitive mechanical or electronic components in the various sensible production. The mobile cleanroom workstation CleanBoy®, for example, enables users to create cleanroom conditions in any work area with effective results at low investment costs.
The CleanBoy® consists of a laminar flow module SuSi® (Super Silent) and a carrying frame made of anodized aluminium profiles. The air is aspirated from the ambient air via a pre-filter, filtered through a high-performance filter of type H14 and directed laminar over the workplace. The filter has a separation efficiency of 99.995%, i.e. the filter separates at least 99.995% of all particles with a particle size of 0.12 μm (according to MPPS). You therefore work under ISO 5 clean room conditions on the tabletop of the unit.
By using the CleanBoy® in a large, walk-in clean room, a limited space is created where practically no particles can be detected. The device is available as a tabletop and floor-mounted unit on wheels. It requires no installation and is ready for use immediately after delivery.
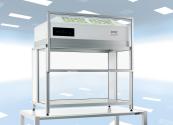
Increasing threat to product characteristics due to particulate matter
Particulate matter consists of a complex mixture of solid and liquid particles and is divided into different fractions according to the particle size. A distinction is made between PM10 and PM2.5 (PM = particulate matter) with a maximum diameter of 10 and 2.5 micrometers (µm) respectively, and ultra-fine particles with a diameter of less than 0.1 µm.
Particulate matter is released from a variety of sources. These include domestic heating and power generation plants, business operations, industrial plants and especially road traffic (diesel soot, abrasion from tires and brakes). Mean annual PM10 values between 15 and 20 µg/m³ are common today, with a trend towards decreasing concentrations being observed. However, the number of particles is increasing dramatically. In enclosed spaces, smoke from tobacco products, emissions from laser printers (up to 2 billion particles per printed page) and humans themselves are sources of particulate matter pollution. The deleterious effects on health of particulate matter vary depending on the size and penetration depth of the particles. They range from mucous membrane irritation and local inflammation in the trachea or bronchi to increased plaque formation in the blood vessels. In order to protect human health, strict annual average limits of 25 µg/m3 therefore apply to PM2.5 particles. As of 2015, adherence to this limit has been mandatory, with the exception that the daily mean PM10 value of 50 µg/m³ may be exceeded up to 35 times per calendar year.
Particulate matter is also posing an increasing threat to many technical processes. In production and packaging, it can alter or impair the properties of products and even destroy optical and electronic components! This is the reason why certain products must be protected from particulate matter under clean room conditions. However, extracting particulate matter is a major technical challenge. Particulate matter can only be removed from the air by properly cleaning the air in the room.
In this context, filter technologies in particular have proven to be a cost-effective alternative. They can be easily retrofitted as needed. This applies equally to complex clean rooms and to smaller filter units, known as laminar flow boxes, because both systems are based on the same filter technology.
A laminar flow box, for example, such as the FBS series from Spetec GmbH, a filter technology manufacturer with decades of experience, uses high-performance class H14 filters. This allows 99.995 % of all particulate matter to be efficiently filtered out (based on a particle size of 0.12 μm)[1]. In this way, the air quality in the interior can be improved by at least 10,000 times compared with the ambient air in the production area. The use of a laminar flow box is an effective measure in the fight against the increasing number of particles. In other words, the most effective way of ensuring the quality and correct operation of products is to use a clean-room workspace.
[1] Certified by the Fraunhofer Institute for Manufacturing Engineering and Automation and classified as ISO 5 as per EN ISO 14644.